SMT assembly in surface mount technology for printed circuit board production
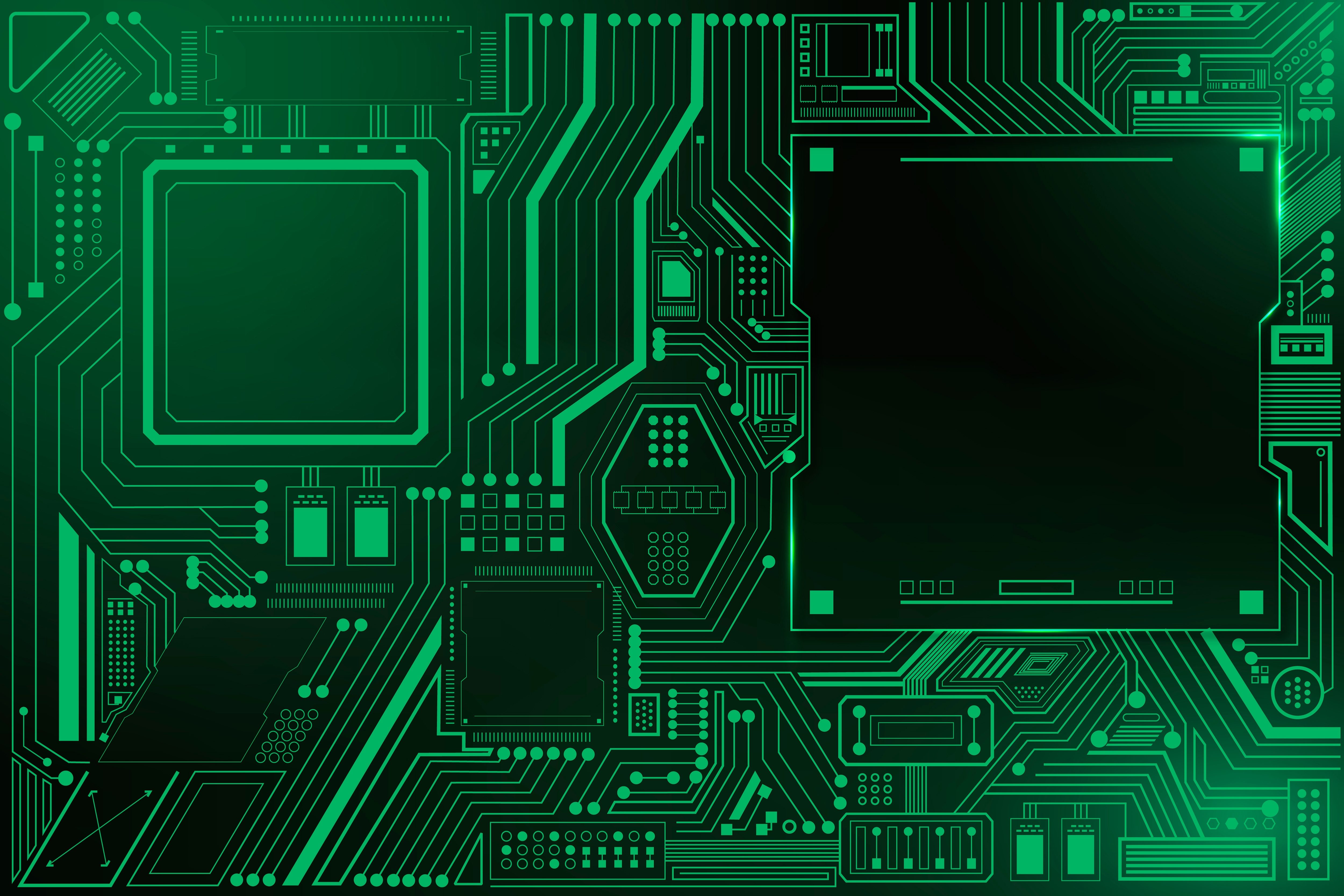
Introduction to SMT assembly and surface-mount technology
The evolution of electronics manufacturing has been shaped by the increasing demand for compact, high-performance, and cost-effective devices. In response to these challenges, Surface Mount Technology (SMT) has emerged as the dominant method for the assembly of printed circuit boards (PCBs). By enabling the placement of components directly onto the surface of the PCB rather than inserting leads into holes, SMT has redefined the efficiency, scalability, and precision of electronic assembly processes.
This introduction provides essential context for understanding the SMT assembly process by outlining its development, comparing it with through-hole technology, and exploring its implications for modern electronics manufacturing.
Evolution of surface mount technology in PCB manufacturing
Surface Mount Technology originated in the 1960s but gained industrial momentum in the 1980s as electronic products began to demand smaller footprints and higher component densities. Traditional through-hole methods, which involved inserting component leads into drilled holes, proved increasingly inefficient in meeting these emerging requirements.
SMT introduced a radical shift by allowing electronic components to be mounted directly onto the surface of the PCB, eliminating the need for hole drilling and significantly reducing the space required on the board. This advancement made it possible to develop multilayer PCBs with dense routing and higher electrical performance, opening the door to innovations in computing, telecommunications, and consumer electronics.
The adoption of SMT was also driven by the rise of automation in assembly lines, where pick-and-place systems and reflow soldering provided faster and more consistent production outcomes. The manufacturing process became more controllable and repeatable, especially when paired with inspection technologies such as AOI and SPI, which ensured high quality at every stage.
SMT vs through-hole technology in modern board assembly
While both SMT and Through-Hole Technology (THT) are used in PCB manufacturing, their roles and applications have diverged significantly. THT remains valuable in specific cases, particularly in power electronics or applications requiring mechanical strength, but its usage has diminished in favor of SMT due to inherent limitations in scalability and miniaturization.
SMT offers several distinct advantages: higher component density, improved signal integrity due to shorter interconnects, and greater suitability for high-speed automated assembly. These benefits translate into reduced production time, lower material costs, and the ability to manufacture smaller, lighter, and more complex devices.
However, the choice between SMT and THT is not always binary. Hybrid approaches are sometimes used in PCB design, especially in prototypes or specialized circuit boards where both mounting techniques offer complementary strengths. Still, for the vast majority of modern electronics, SMT assembly has become the industry standard due to its superior adaptability and efficiency.
SMT assembly process overview
Understanding the full scope of the SMT assembly process is essential for evaluating the precision, repeatability, and quality that modern electronics manufacturing demands. From the moment a bare PCB enters the SMT line to the final inspection of the assembled product, each stage plays a critical role in ensuring functional and reliable circuit boards. This section presents a structured overview of the SMT assembly process, describing both the macro-level flow and the detailed operations that define successful outcomes.
The SMT line is designed to perform a sequence of operations with minimal interruption and maximum automation. These operations include solder paste deposition, component placement, reflow soldering, and inspection, each contributing to the overall integrity of the board assembly.
SMT line structure and function
An SMT line typically consists of a series of integrated machines working in sequence to assemble electronic components onto the surface of PCBs. This automated line minimizes human intervention, allowing for consistent performance and increased throughput.
The process generally begins with the solder paste printer, which applies a defined volume of solder paste to each pad on the board using a stencil. The PCB then proceeds to a pick-and-place machine, which positions components with high speed and precision. After placement, the board enters a reflow oven, where the solder paste is melted to form electrical and mechanical connections.
Throughout the SMT line, auxiliary systems such as conveyors, loaders, and unloaders ensure smooth handling of the boards. Vision systems embedded within the machines verify alignment, placement accuracy, and other parameters in real time. The efficiency and reliability of the SMT line directly impact the quality of the final product and the cost-effectiveness of the assembly process.
Key stages of the SMT assembly process
The SMT assembly process is composed of four fundamental stages: solder paste application, component placement, reflow soldering, and inspection. Each of these stages must be carefully controlled and optimized to maintain yield and avoid defects.
The first step, solder paste application, uses a stencil and printer to deposit paste onto the PCB pads. The stencil design and paste properties are critical to ensuring the right amount of solder is applied uniformly. Inaccuracies at this stage can lead to bridging, insufficient solder, or open joints.
Next, during the component placement stage, surface-mount components are picked from reels or trays and placed on the solder-pasted PCB. Modern machines offer exceptional placement accuracy, which is especially important for fine-pitch packages and miniature components.
The reflow soldering stage subjects the populated PCB to a controlled thermal profile in a reflow oven. The solder paste melts and forms joints, after which it solidifies upon cooling. Factors such as ramp rate, peak temperature, and dwell time influence joint quality and must be tailored to the board and component specifications.
Finally, inspection often using Automated Optical Inspection (AOI) systems verifies solder joint integrity, component alignment, and the presence of all required parts. This stage is vital in identifying process variations early, reducing rework and improving long-term reliability.
Solder paste application and inspection
Solder paste plays a foundational role in the SMT assembly process, serving both as the electrical and mechanical link between the SMT components and the printed circuit board. Its correct application is essential for ensuring the integrity of each solder joint and, ultimately, the reliability of the entire circuit. Misapplication or defects in solder paste can lead to critical failures, including opens, shorts, or weak mechanical connections. This section focuses on the importance of stencil design, solder paste properties, and the methodologies used in solder paste inspection.
Role of stencil design in solder paste application
The stencil is a precision-engineered tool that defines where and how much solder paste is deposited on the PCB. Typically made from stainless steel and fabricated using laser-cutting technology, the stencil contains apertures aligned with the pad layout of the PCB. When solder paste is applied using a squeegee, it is forced through the apertures onto the board's surface.
The accuracy of stencil design has a direct impact on the success of the assembly process. Aperture dimensions, wall smoothness, and stencil thickness must be optimized based on the pad geometry, component type, and desired paste volume. For fine-pitch components and high-density interconnects, stencil technology must achieve a high level of precision to prevent issues such as bridging or insufficient solder volume.
Proper stencil design also accounts for factors like solder paste rheology and board layout. In complex PCB designs, features such as step-down or multi-level stencils may be necessary to accommodate components with varying paste requirements.
Solder paste characteristics and quality parameters
Solder paste is a suspension of metal alloy particles in a flux medium, and its performance depends on both chemical and physical properties. Key parameters include viscosity, particle size distribution, metal content, and flux activity. These attributes influence how the paste behaves during printing, component placement, and reflow.
High-quality solder paste must maintain its consistency throughout the production process, resisting slumping or drying while still offering good wetting characteristics during reflow. It must also provide sufficient tackiness to hold components in place between placement and soldering.
Environmental conditions such as humidity and temperature can affect solder paste stability. Therefore, storage, handling, and application procedures must be carefully controlled to prevent contamination and degradation. In high-reliability applications, paste selection is subject to strict validation procedures and compliance with international standards such as IPC specifications.
Solder paste inspection (SPI) techniques and standards
Solder paste inspection is a critical control point in the SMT process. Using 3D SPI systems, manufacturers can measure volume, height, and area of the deposited paste with micrometer-level accuracy. This quantitative data helps identify issues like insufficient, excessive, or misaligned deposits before they propagate downstream.
SPI systems typically rely on structured light or laser triangulation to construct a three-dimensional profile of each solder deposit. These measurements are compared to predefined thresholds derived from the PCB design and component footprint. Deviations outside acceptable limits trigger alerts or halt production for correction.
By integrating SPI early in the SMT line, manufacturers can reduce defect rates, improve yield, and optimize print parameters in real time. Modern systems can also perform statistical analysis to detect trends that may indicate stencil wear, paste aging, or equipment drift. Implementing robust solder paste inspection protocols is thus essential for achieving consistent quality in high-volume PCB assembly.
Component placement in SMT assembly
Component placement is the stage in the SMT assembly process where surface-mount devices are accurately positioned onto the solder-pasted printed circuit board. This operation is performed with high precision and speed using automated pick-and-place systems that are a central element of every SMT line. The reliability of the final electronic assembly depends heavily on this phase, as any misalignment or handling error can result in functional defects or mechanical failures.
Modern SMT placement systems combine mechanical accuracy with intelligent vision systems and data-driven control, making it possible to handle a vast variety of component shapes, sizes, and packages from large connectors to micro-scale passive devices.
High speed pick-and-place systems on SMT lines
Pick-and-place machines are designed to rapidly transfer electronic components from feeder mechanisms onto PCBs. These machines use vacuum nozzles to pick components from reels, trays, or tubes, and place them precisely on the designated solder paste deposits.
High-speed placement heads are capable of handling thousands of components per hour, which is essential in large-scale PCB production. Modern systems integrate multiple nozzles, each independently controlled, to achieve parallel processing and reduce cycle time.
The machine’s motion is guided by a combination of mechanical encoders, servo motors, and vision systems that verify component orientation and placement coordinates in real time. Component recognition is typically performed using cameras that compare the captured image with reference models, ensuring both correct identification and orientation.
Adaptability is also key. SMT lines must accommodate various board sizes and layouts, often switching between different production batches. Therefore, pick-and-place equipment supports rapid changeovers and offline programming, which allows the SMT assembly process to remain flexible and efficient even in high-mix production environments.
Placement accuracy and component handling
Placement accuracy is measured in microns and is critical for maintaining the electrical and mechanical integrity of surface-mounted devices. As PCB designs evolve to include finer pitches and denser layouts, the precision of the placement process becomes increasingly important.
Several factors influence placement accuracy: machine calibration, nozzle condition, vision alignment, and board flatness. Routine maintenance and environmental control are essential to minimize sources of error such as vibration, dust, or thermal expansion.
Component handling must also be executed with care. Delicate components such as ceramic capacitors or miniature ICs can be damaged by improper mechanical force or electrostatic discharge. Advanced pick-and-place systems apply just enough force to secure the component without compromising its structure or function.
In addition, feeder performance impacts the continuity and quality of the assembly line. Feeders must deliver components consistently, with accurate indexing and minimal variation, to ensure uninterrupted placement.
Considerations in printed circuit board assembly for complex components
The placement of complex SMT components such as BGAs, QFNs, or components with irregular shapes introduces unique challenges that require advanced process control. These packages often have hidden or bottom-terminated leads, making visual inspection and alignment more difficult.
To address these issues, pick-and-place machines use high-resolution vision systems and fiducial alignment to ensure exact positioning. Some components may also require support mechanisms or tooling during placement to maintain co-planarity and avoid tilting or warping.
PCB design must also support proper placement. Sufficient pad spacing, accurate footprints, and optimized land patterns are necessary to prevent misalignment and ensure correct solder joint formation during reflow. In high-reliability applications, engineers may use X-ray inspection post-reflow to verify joint quality, especially for hidden terminations.
Component placement is not only a mechanical task but a process that integrates software, vision, and materials knowledge. By understanding and controlling all these variables, manufacturers can achieve consistent results and minimize assembly-related failures.
Reflow soldering in PCB assembly
Reflow soldering is the process that permanently bonds SMT components to the printed circuit board by melting the solder paste previously deposited during the printing stage. It is one of the most critical phases in the SMT assembly process because it directly determines the mechanical strength and electrical conductivity of solder joints. Reflow must be precisely controlled to avoid defects such as cold joints, tombstoning, or component damage due to thermal stress.
The process involves heating the entire populated PCB in a controlled thermal environment to reflow the solder particles, allowing them to wet the component leads and pad surfaces before cooling down to solidify the connection.
Thermal profiling and soldering parameters
Thermal profiling is essential in defining the optimal temperature-time curve that a PCB must follow during reflow. This profile is influenced by factors such as the size and thermal mass of the board, the type of solder paste used, and the component mix. A well-defined thermal profile ensures uniform heating, proper wetting, and avoidance of thermal shock.
The typical reflow profile consists of four main stages: preheat, soak, reflow, and cooling. In the preheat stage, the board is gradually brought up to temperature to reduce thermal shock. The soak zone allows for temperature stabilization and activation of the flux. The reflow stage is where the solder reaches its liquidus point, allowing the metallurgical bond to form. Finally, controlled cooling solidifies the joints and minimizes stress.
Peak temperature and time above liquidus are critical parameters. If the temperature is too low or the time too short, solder may not fully melt, resulting in weak joints. Conversely, excessive heat can damage components or cause solder to oxidize, reducing joint reliability.
Different solder alloys, such as SAC305 or low-temperature formulations, require tailored profiles. Therefore, thermal profiling is usually validated using thermocouples and recorded with profiling tools to ensure compliance with the specifications of both the solder paste and the components.
Impact of reflow process on solder joint reliability
The reflow process plays a defining role in the overall quality of solder joints. A properly executed reflow cycle results in smooth, shiny, and uniformly wetted joints that ensure both mechanical stability and low-resistance electrical connections. However, even slight deviations in the process can introduce a range of defects that compromise the assembly.
Common issues include voiding within the solder joint, insufficient wetting, or overheating of sensitive components. Voids, particularly in power devices or BGAs, can lead to increased thermal resistance and long-term reliability concerns. Oxidation and flux residues may also interfere with joint formation if the reflow environment is not adequately controlled.
Modern reflow ovens employ multi-zone temperature control and nitrogen atmospheres to improve consistency and reduce oxidation. Proper reflow not only enhances immediate joint quality but also improves long-term performance in environments involving vibration, thermal cycling, or mechanical stress.
Ultimately, the effectiveness of the reflow soldering stage depends on close coordination with upstream processes — including stencil design, solder paste selection, and component placement making it a central element of a well-optimized SMT line.
Automated optical inspection (AOI) in SMT lines
Automated Optical Inspection (AOI) is a vital step in the SMT assembly process, serving as a non-contact, high-speed method for detecting surface-level defects on assembled printed circuit boards. Positioned after critical stages such as solder paste printing and reflow soldering, AOI systems perform detailed visual analysis to verify component placement, solder joint quality, and the overall assembly accuracy. This allows manufacturers to identify and correct issues early, reducing rework costs and enhancing production yield.
The integration of AOI in modern SMT lines reflects the industry's commitment to zero-defect manufacturing, especially as circuit complexity and component miniaturization continue to increase.
Principles of AOI in PCB manufacturing
AOI systems use a combination of high-resolution cameras, structured lighting, and image processing algorithms to inspect PCBs at various stages of the assembly line. These systems capture images of the board and compare them to reference data, such as golden board images or CAD-derived models, to detect deviations.
AOI is capable of identifying a wide range of defects, including missing components, misalignment, incorrect orientation, tombstoning, solder bridges, and insufficient or excessive solder. These inspections can be performed in both 2D and 3D formats, with 3D systems offering improved depth analysis for features such as solder joint height and volume.
Inspection parameters are defined during the programming phase, where acceptable tolerances are set based on component type, footprint, and manufacturing requirements. AOI machines can inspect hundreds of components in seconds, making them essential for high-throughput production environments.
Benefits of AOI in early defect detection
Incorporating AOI into the SMT assembly process significantly improves quality control by enabling real-time detection of process deviations. Catching defects early especially after solder paste printing or component placement prevents faulty boards from reaching later stages of production where correction is more difficult and expensive.
Early-stage AOI, such as post-print inspection, ensures that solder paste has been applied correctly in terms of position, volume, and height. This reduces the likelihood of joint-related defects in subsequent steps. Mid-line AOI after placement confirms that components are present, correctly oriented, and properly aligned before reflow soldering. Post-reflow AOI assesses the final state of solder joints and component conditions.
Another key advantage is data collection. AOI systems generate detailed inspection records that can be used for statistical process control and continuous improvement. By analyzing trends in defect types and frequencies, manufacturers can fine-tune their SMT lines to reduce variability and improve consistency.
AOI vs other inspection methods in SMT assembly
While AOI is highly effective for surface-level visual inspection, it complements rather than replaces other inspection methods. For example, Solder Paste Inspection (SPI) is used specifically to assess solder paste deposition prior to component placement, offering volumetric analysis that AOI cannot perform at that stage. Meanwhile, X-ray inspection (AXI) is used for inspecting hidden joints, such as those under BGAs, where AOI cannot access critical features.
Compared to manual inspection, AOI provides far superior consistency, repeatability, and speed. It removes subjectivity from the inspection process and allows for 100% inspection coverage without compromising throughput.
However, AOI has limitations. It cannot assess internal or non-visible defects, and it may generate false positives if tolerances are not accurately defined. For this reason, it is often used in conjunction with other techniques as part of a comprehensive quality assurance strategy in PCB assembly.
Surface mount technology advantages in modern electronics
Surface Mount Technology has become the backbone of modern electronics manufacturing due to its ability to support increasingly complex circuit designs while maintaining scalability, precision, and cost efficiency. As devices become smaller, faster, and more interconnected, the advantages of SMT over legacy techniques such as through-hole assembly are more pronounced than ever. This section outlines the primary benefits of SMT in the context of today's electronic production demands, focusing on miniaturization, production economics, and overall performance enhancement.
Miniaturization and assembly efficiency
One of the most transformative advantages of SMT is its ability to support miniaturization. Unlike through-hole components, SMT components do not require lead insertion through drilled holes, allowing them to occupy far less board space. This enables designers to create highly compact printed circuit boards without sacrificing functionality.
The surface mounting of components also permits placement on both sides of the PCB, further improving space utilization. High-density interconnect (HDI) techniques, facilitated by SMT, allow for increased circuit complexity within smaller physical dimensions a key requirement in portable and embedded systems.
In addition to physical space savings, SMT significantly enhances assembly efficiency. Automated pick-and-place systems can handle thousands of components per hour with micron-level accuracy. The elimination of manual lead insertion speeds up the production process and reduces labor requirements. As a result, SMT shortens time-to-market while enabling the reliable assembly of complex, multilayer PCBs.
Cost-effectiveness in high-volume production
SMT offers clear cost benefits, especially in high-volume manufacturing environments. Automated SMT lines are designed to produce large quantities of PCB assemblies with minimal variation and low per-unit cost. The scalability of SMT processes allows for efficient allocation of fixed costs across large production runs, which is especially advantageous in consumer electronics and telecommunications sectors.
Component costs are also optimized with SMT. Surface-mount devices are typically smaller and more standardized than their through-hole counterparts, resulting in lower material and shipping costs. In addition, the reduced need for drilling and manual labor further decreases production expenses.
Yield improvement is another contributor to cost efficiency. With precise solder paste application, accurate component placement, and reliable reflow soldering, SMT minimizes defect rates. Integrated inspection technologies such as SPI and AOI help maintain consistent process quality, reducing waste, rework, and field failures.
Over time, the combination of automation, reduced material usage, and lower defect rates results in a robust manufacturing process that supports competitive pricing without compromising product quality.
Reliability and electrical performance improvements
Beyond size and cost, SMT improves the reliability and electrical performance of circuit boards. Shorter interconnect paths between components reduce parasitic inductance and capacitance, which is particularly beneficial in high-frequency and high-speed circuits. These characteristics help ensure signal integrity and electromagnetic compatibility.
Mechanical reliability is also enhanced due to the lower mass of SMT components and the strength of surface-mounted solder joints. SMT assemblies are more resistant to vibration, shock, and thermal cycling essential attributes for automotive, aerospace, and industrial applications where harsh operating conditions are common.
The repeatability of SMT processes further ensures consistent solder joint quality. Controlled reflow profiles and real-time inspection minimize the risk of hidden defects such as cold joints or voids. When properly designed and manufactured, SMT-based PCBs exhibit extended operational lifespans and improved field reliability.
In the context of modern electronics, where performance, size, and dependability are all critical, SMT provides the manufacturing foundation that enables innovation without sacrificing quality.
Conclusion
Surface Mount Technology has redefined the way electronic devices are manufactured, enabling a level of precision, scalability, and reliability that traditional methods could not achieve. From the application of solder paste to the final stages of automated optical inspection, each element of the SMT assembly process contributes to the production of highly functional, densely populated, and robust printed circuit boards.
Through this detailed exploration of SMT assembly, it becomes evident that the integration of automated systems, data-driven inspection, and optimized material usage forms a cohesive and efficient manufacturing process. SMT not only accommodates the growing demand for miniaturized electronics but also supports rapid production cycles and consistent product quality at scale.
The advantages of SMT including assembly efficiency, reduced production costs, and superior electrical performance are central to its dominance in modern electronics manufacturing. Whether applied to consumer electronics, telecommunications, medical devices, or industrial systems, SMT provides the structural and functional backbone required for innovation and long-term reliability.
As electronic design continues to evolve, SMT will remain a cornerstone of printed circuit board assembly, offering the technological foundation needed to meet both current and future industry requirements. Manufacturers who understand and effectively implement SMT principles position themselves at the forefront of precision electronics production, capable of delivering performance-driven solutions in an increasingly demanding market.